In this article, we have explained 7 highly effective means of improving and enhancing the manufacturing process. But, let’s first understand some important things.
In today’s world of science and technology, industrial production managers chase after targets and goals to take the manufacturing process to the zenith. With facts and figures changing year to year, goals are set to reach targets, increase labour, enhance R&D, reduce direct costs, and improve the overall manufacturing process. Embracing new technologies, strategies, and AI-based methodologies makes it possible to make positive, significant changes in the manufacturing sector.
Manufacturers and production managers now rely on measured and incremental steps to take the numbers to a higher notch. The ultimate objective is to increase production, deliver using effective and efficient machine-hours, reduce waste, and cut unnecessary interruptions and idle hours. This leads to automation and optimization.
Why Improve the Manufacturing Process?
- To enhance the product quality and optimize the cost. Better products are easier to market, thus helping in improving market credibility and it leads to customer satisfaction. Market credibility is a great way towards gaining a competitive advantage.
- To cut off inefficient ways of working, scraps generated and resolving bottlenecks, all of which are proportional to achieving higher productivity. Overall improvement in the production can be a great boost to employees’ morale.
However, building a culture of improvement is possible once you understand the entity.
Understanding the Business
The first and foremost objective is to understand the organisation and learn about its business. This includes acknowledging its vision, mission, objectives, and goals. You can accomplish this by the following-
- Know about KPIs (key performance indicators).
- Set a target and bridge the gap between the present state of manufacturing performance and future by formulating strategies.
- Make sure the strategies are clear, concise, not vague, achievable, realistic, and deterministic.
- Learn about existing core consistencies and leadership capabilities.
- Do a SWOT and PEST analysis to understand your business and strategize accordingly.
- Create and base your decisions on performance measurement metrics to achieve your goals.
Next, let’s understand what you can do to improve your manufacturing process..
7 Proven Strategies to Improve Manufacturing Process Efficiency:
1. Analyze the Current Workflow and Identify Loopholes
It is important to analyze the current workflow, which includes the following (the list is inclusive and not exhaustive):
- Processes: Know what all the critical factors, bottlenecks, and obstacles are. Evaluate the process and chart out to understand the workflow.
- Personnel: Evaluate the present personnel based on how smart, efficient and diligent they are. Mind whether segregation of duties is done appropriately. Make sure the objectives set for the personnel are achievable, realistic, time-based, measurable, specific, and assignable.
- Tools and technology: Study the technology used and tools equipped for various production processes. Among these tools, web guiding systems play a crucial role in ensuring accuracy and precision in many industries. See if the machines are up to the mark and are reliable. Make sure the technology is not outdated and meets all business needs. Evaluate the machinery cost, repair expenses, and maintenance costs.
Make sure you identify the loopholes and categorize the problems in three levels, namely:
- Weaknesses in business process
- Individual employees’ performance flaws
- Organizational structure loophole
2. Use Advanced Technologies and Methodologies
It is critical to modernizing your technology and process. Make sure you use the most advanced technologies, and methodologies to structure your production, save time, optimize resources. You will have to use advanced software to modernize every aspect of planning, inventory control and monitoring overall procedures. You can do this through robotic process automation, also denoted as RPA. It involves using standardized software such as the Rootstock ERP to automate labor-intensive tasks and limit employees’ repetitive tasks.
Moreover, this is also possible by leveraging business intelligence data (BI generated data), which directly impacts the supply chain and manufacturing processes. Examining such crucial data can help managers, strategists, and technicians learn about inefficiencies and understand why production is not as effective as planned.
Also, record the overall cost of ownership, other capital costs, R&D, and other intangible expenses.
3. Develop Employee Training and Engagement Programs
Labour is a critical part of manufacturing process. Every production unit must have skilled labour. To optimize your manufacturing, it’s necessary that your workers shorten their learning curves, gain adequate knowledge and skills, have sufficient expertise, and reduce idle time to achieve efficiency.
The above is possible by training staff, providing sessions and courses to gather skills, and frequently providing refresher courses to guide how to use a machine or handle the equipment. Also, you should learn about lean manufacturing production method.
You May Like: How to Be an Effective Construction Project Manager
4. Never Ignore Routine Maintenance
Maintenance is necessary to make sure production does not perform poorly. Imagine an outdated machine that costs worn-out machinery costs thus, affecting the overall manufacturing costs.
To take up planned maintenance, you will have to note down the following:
- Train your operators and technicians to sharpen their skills to fix whenever a problem arises with a machine or a system.
- Fix a time and schedule the maintenance of your system- your hardware and your software. Updating it regularly is of maximum priority.
- Never skip any update.
- Keep a note of the repair and maintenance costs.
See Also: How Do You Ensure Safety and Security of Employees?
5. Use Cloud-Based Systems to Connect Supply Chain
Enterprises with multiple suppliers across the globe make it challenging to sync and control the workflow process. You can establish a network between the various supply chain links to keep a tab on these units and facilities. You can even have quality assurance reviewers and inspectors review operations and organize them systematically on the database.
Nowadays, enterprises rely on private clouds, wherein everything is connected and synced. This eases the overall system and makes it flexible. Employees can even access tools and data across remote locations present on the webserver through cloud computing technology.
6. Go For a Work Order Ticket System
Many organizations are now switching to a work order management system. The process relates to receiving requests upon orders generated internally or created by a customer. The system helps in clarifying all work to be done, sets a targeted deadline, renders specific instructions, and helps the organization maintain and manage resources, data, expenses, and labour.
These tactical solutions help ineffective management and overall optimization of the manufacturing process.
7. Track Wastage and Find a to Reduce It
Cutting on scraps and reducing waste generation is crucial to improving productivity and increasing the overall margin. Wasted material is one of the most critical expenses in today’s economy. To keep an eye on conserving resources, asset management, and waste management, one must check on each production process.
Process evaluation can lead to identifying and determining what all processes generate the maximum scratch. Finding effective control can lead to waste and cost reduction.
Inventory control, modern tool usage, data logging are some of the ways to achieve this objective. Make sure the defects do not pile up.
There are various other means to boost your manufacturing process, such as deploying new tools, using new software and hardware, quantifying outcomes, etc. which assures continuous improvement in the relevant sector.
The provision of adequate and advanced tools will not only ease the work process but also encourage employees. It will inspire them to generate effective hours and improve productivity.
Conclusion
In the article, you came across powerful strategies that can help you optimize your production process. You must structure your processes, train your staff, maintain the system, and pick the best production processes to improve your manufacturing processes.
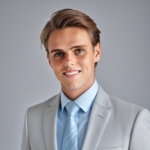
Hi there! I’m Nick Cullen. As the Senior Content Editor with Solution Suggest, my responsibility is to scrutinize and refine our articles and reviews, focusing on software solutions, games, apps, and websites. I’m dedicated to delivering reliable and enlightening content that offers viable alternatives to your current digital tools. If you have any suggestions or inquiries, you can reach me at editor@solutionsuggest.com. Also, I invite you to connect with me on LinkedIn!
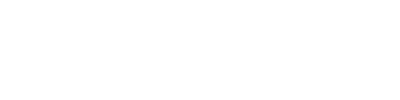