In the realm of logistics and supply chain management, cross-docking stands out as a strategy that’s increasingly gaining traction. This guide offers a thorough exploration of cross-docking, highlighting how it can enhance your logistics strategy with its benefits, challenges, and practical examples.
Cross Docking Explained
Cross docking is a supply chain management technique where incoming goods from suppliers are directly unloaded from inbound transportation vehicles (such as trucks or trailers) and loaded onto outbound vehicles with little to no storage in between. Essentially, it’s a method that bypasses the traditional warehousing model where goods are stored for a period before being shipped out.
Benefits of Cross Docking
1. Efficient Loading and Unloading Strategies
Cross docking eliminates the need for storing goods in warehouses, thereby reducing the time and resources required for loading and unloading. With goods moving directly from inbound to outbound transportation, there’s a significant reduction in handling time. This efficiency translates into lower labor costs and faster turnaround times, ultimately enhancing overall operational efficiency.
2. Reducing Handling Costs
Traditional warehousing involves multiple touchpoints and handling processes, which can incur substantial costs. Cross docking streamlines these processes by minimizing or eliminating the need for storage, consolidation, and picking, thereby optimizing your operations. By reducing handling steps, businesses can significantly lower their handling costs, leading to cost savings that can be reinvested into other areas of the supply chain.
3. Improving Transportation Efficiency
One of the primary advantages of cross-docking is its ability to optimize transportation routes and schedules. By consolidating shipments and minimizing storage time, cross-docking ensures that goods reach their destinations more quickly and efficiently. This not only reduces transit times but also lowers transportation costs, as fewer resources are needed to move goods from point A to point B.
4. Warehouse Space Optimization
Traditional warehouses require ample space for storing inventory, which can be costly to maintain and manage. Cross-docking eliminates the need for large storage areas, allowing businesses to optimize their warehouse space for other purposes or even downsize their facilities. This not only reduces leasing or ownership costs but also maximizes the use of available space, improving overall resource utilization.
Learn More about Warehouse Optimization Software.
5. Minimizing Storage Time
In traditional warehousing models, goods may spend days or even weeks sitting on shelves before being shipped out. This prolonged storage time not only ties up capital but also increases the risk of damage, spoilage, or obsolescence.
Cross-docking minimizes storage time by facilitating direct transfer of goods from inbound to outbound transportation, reducing the likelihood of inventory-related issues and improving inventory turnover rates.
Must Read: Impressive Facts About Industrial Tents
Challenges in Cross-Docking
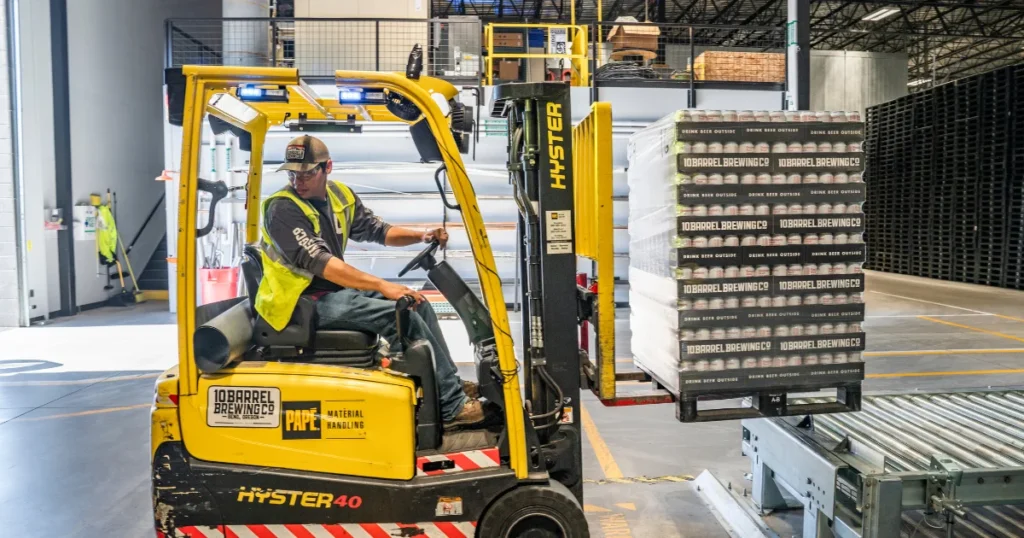
1. Supply Chain Synchronization
Cross-docking relies heavily on precise timing and coordination among various stakeholders within the supply chain. Ensuring that suppliers, transportation providers, and distribution centers are synchronized to facilitate seamless inbound and outbound flows of goods can be a significant challenge. Delays or disruptions at any point in the chain can lead to inefficiencies and disruptions in the cross-docking process.
2. Streamline Distribution Processes
Efficiently managing the flow of goods and information in cross-docking operations requires streamlined distribution processes. This involves accurately sorting, consolidating, and routing products to their respective outbound destinations. Managing diverse product types, varying shipment sizes and complex routing requirements can complicate these processes and increase the risk of errors or inefficiencies.
3. Just-in-Time Shipping Methods
Cross-docking often operates on a just-in-time (JIT) basis, where goods are transferred directly from inbound to outbound transportation without storage in between. Achieving JIT shipping requires precise coordination and scheduling to align inbound arrivals with outbound departures.
Factors such as variable lead times, unpredictable demand fluctuations, and external disruptions (e.g., weather, traffic) can challenge the ability to maintain JIT shipping schedules.
4. Inventory Reduction Strategies
One of the primary goals of cross-docking is to minimize inventory holding costs by reducing the time products spend in storage. However, effectively managing inventory levels without the safety net of storage facilities presents a challenge.
Organizations must accurately forecast demand, optimize order quantities, and coordinate replenishment cycles to prevent stockouts while avoiding excess inventory buildup.
5. Enhancing Operational Throughput
Maximizing the efficiency of cross-docking operations requires ongoing efforts to enhance operational throughput. Enhance your operations by optimizing workflow processes, leveraging technology and automation, and investing in infrastructure improvements.
However, increasing throughput while maintaining accuracy and quality standards can be a complex endeavor, requiring continuous improvement initiatives and strategic investments.
Must Read: How Do You Ensure Safety and Security of Employees?
Cross-Docking Logistics
Cross-docking logistics encompass the intricate processes and strategies involved in efficiently managing the flow of goods through a cross-docking facility.
It’s not merely about transferring products from inbound to outbound transportation but also about optimizing every step of the journey to ensure seamless operations and maximum efficiency.
Cross-Docking Warehouse Design
The foundation of effective cross-docking logistics lies in the design of the warehouse facility itself. A well-designed cross-docking warehouse layout is crucial for facilitating smooth material flow and minimizing bottlenecks. This involves:
- Layout Optimization: Designing the layout to minimize travel distances for both workers and goods, reducing handling time and improving overall efficiency.
- Workflow Planning: Developing streamlined workflows that dictate how goods move through the facility, from receiving to shipping, to ensure a logical and efficient process.
- Space Utilization: Maximizing available space while minimizing congestion and clutter to accommodate the high volume of goods moving through the facility.
Lean Warehousing Techniques
Incorporating lean warehousing principles into cross-docking logistics can further enhance efficiency and productivity. These techniques focus on eliminating waste and optimizing processes to achieve continuous improvement. Key aspects include:
- 5S Methodology: Implementing the principles of Sort, Set in Order, Shine, Standardize, and Sustain to organize the workspace, improve visibility, and maintain cleanliness and orderliness.
- Visual Management: Using visual cues such as signs, labels, and color coding to communicate information, streamline processes, and facilitate quick decision-making.
- Kaizen (Continuous Improvement): Encouraging a culture of continuous improvement where employees are empowered to identify and implement small, incremental changes to optimize workflows and eliminate inefficiencies.
By focusing on warehouse design and implementing lean warehousing techniques, businesses can optimize their cross-docking logistics to achieve maximum efficiency and productivity, ultimately driving greater success in their supply chain operations.
Related: How Is Data Analytics Used in Manufacturing?
Conclusion
Cross-docking offers myriad benefits for businesses looking to streamline their distribution processes and improve supply chain efficiency. While it comes with its challenges, leveraging efficient loading and unloading strategies, optimizing warehouse design, and adopting lean warehousing techniques can help organizations unlock the full potential of cross-docking.
By implementing the right ERP system, such as SAP or Tally, businesses can further enhance their cross-docking operations and stay ahead in today’s competitive marketplace.
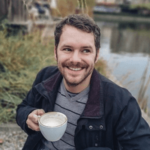
Harry O’Neill writes about all things tech, SaaS, and marketing at Solution Suggest. He’s known for turning complex ideas into clear, actionable insights. With experience working alongside top-tier companies worldwide, he helps brands connect with their audiences through content that drives real results.
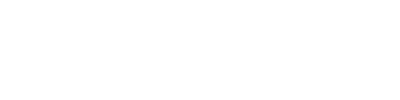