In the dynamic landscape of industrial automation, the spotlight often shines on Automated Guided Vehicles (AGVs) – the silent workhorses revolutionizing logistics and manufacturing processes. Integral to their relentless operation is an aspect often taken for granted: battery charging.
As industries strive for efficiency and sustainability, the choice between wired and wireless charging systems for AGVs stands at the forefront of strategic planning. This extensive exploration delves into the nuances of AGV battery chargers, offering insights to inform the pivotal decision between wired and wireless methodologies.
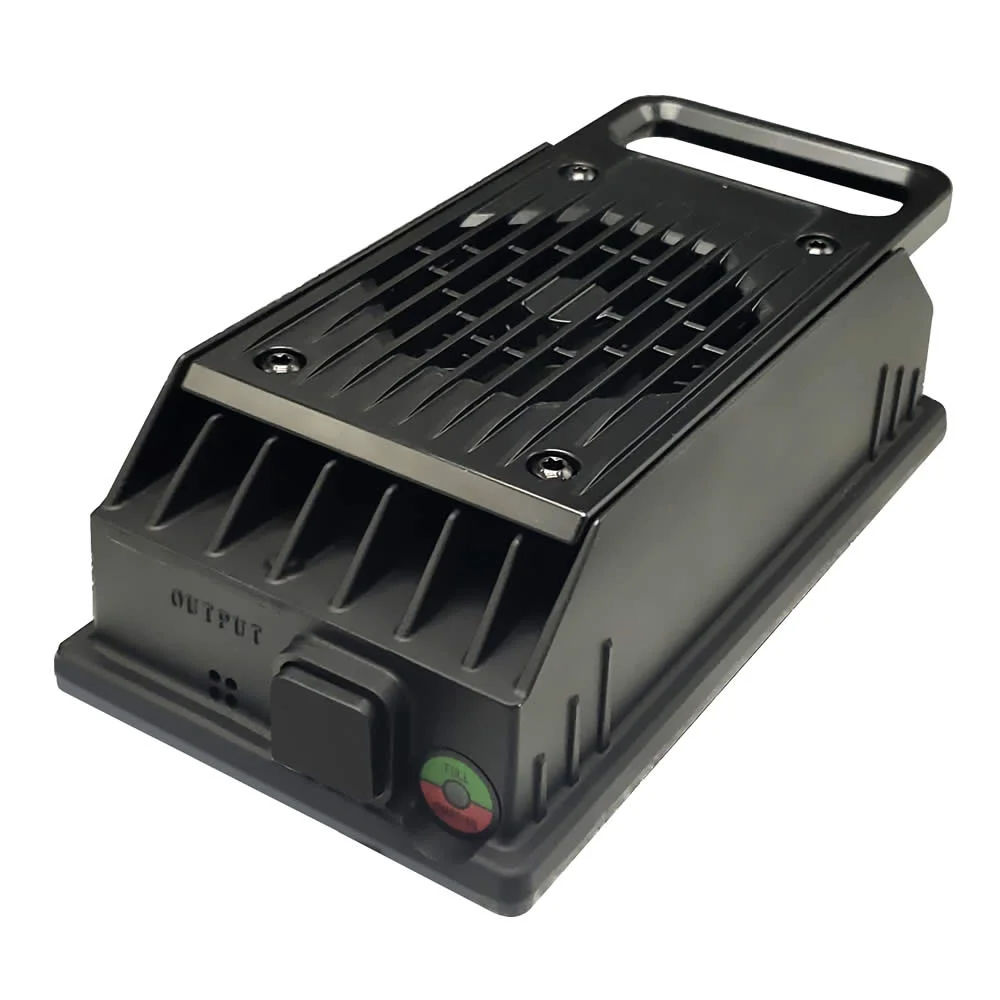
The evolution of AGV technology marks a significant leap towards optimizing operational workflows, with battery charging playing a pivotal role in this transformative journey.
As AGVs become increasingly integral to industries, the method of recharging their batteries – wired or wireless – emerges as a critical consideration. This section illuminates the intricacies of both charging methods, setting the stage for a comprehensive evaluation.
Also Read: Injured in a Car Crash? Here’s Why You Need a Lawyer ASAP
Understanding AGVs and Their Power Needs
What Are Automated Guided Vehicles (AGVs)?
AGVs are sophisticated robots engineered to transport materials around manufacturing facilities or warehouses without human intervention. Their design allows for seamless integration into various operational processes, enhancing efficiency and reducing manual labor.
How Do AGVs Power Their Operations?
At the heart of every AGV is its battery, the source of its mobility and functionality. The efficiency and reliability of AGV operations significantly depend on the battery’s performance and the effectiveness of its charging system.
Types of batteries used: AGVs are typically powered by lead-acid, nickel-metal hydride, or lithium-ion batteries, each with distinct characteristics and applications.
Importance of efficient charging: Ensuring batteries are charged efficiently and reliably is paramount to maximizing the operational uptime of AGVs and minimizing disruptions.
Wired Battery Charging for AGVs
How Does Wired Charging Work?
Wired charging involves physically connecting the AGV to a charging station using cables. This method has been the traditional approach, offering straightforward and reliable means to replenish an AGV’s battery.
Main stages of the wired charging process: The process includes connecting the AGV to the charging dock, initiating the charge cycle, and disconnecting once fully charged, often managed through automated systems.
Types of Wired Charging Systems
Wired charging can vary in complexity and design, ranging from simple plug-in stations to automated conductive charging where connections are made automatically.
Description of each type with pros and cons: While plug-in systems are cost-effective and simple, automated conductive systems reduce manual intervention but at a higher initial investment.
Advantages of Wired Charging
- Predictability and reliability in charging
- Typically lower setup costs compared to wireless systems
- High energy efficiency with direct electrical connections
Limitations of Wired Charging
- Requires AGVs to be out of operation during charging
- Physical wear and tear on connectors and cables
- Limited flexibility in AGV movement and deployment
Wireless Battery Charging for AGVs
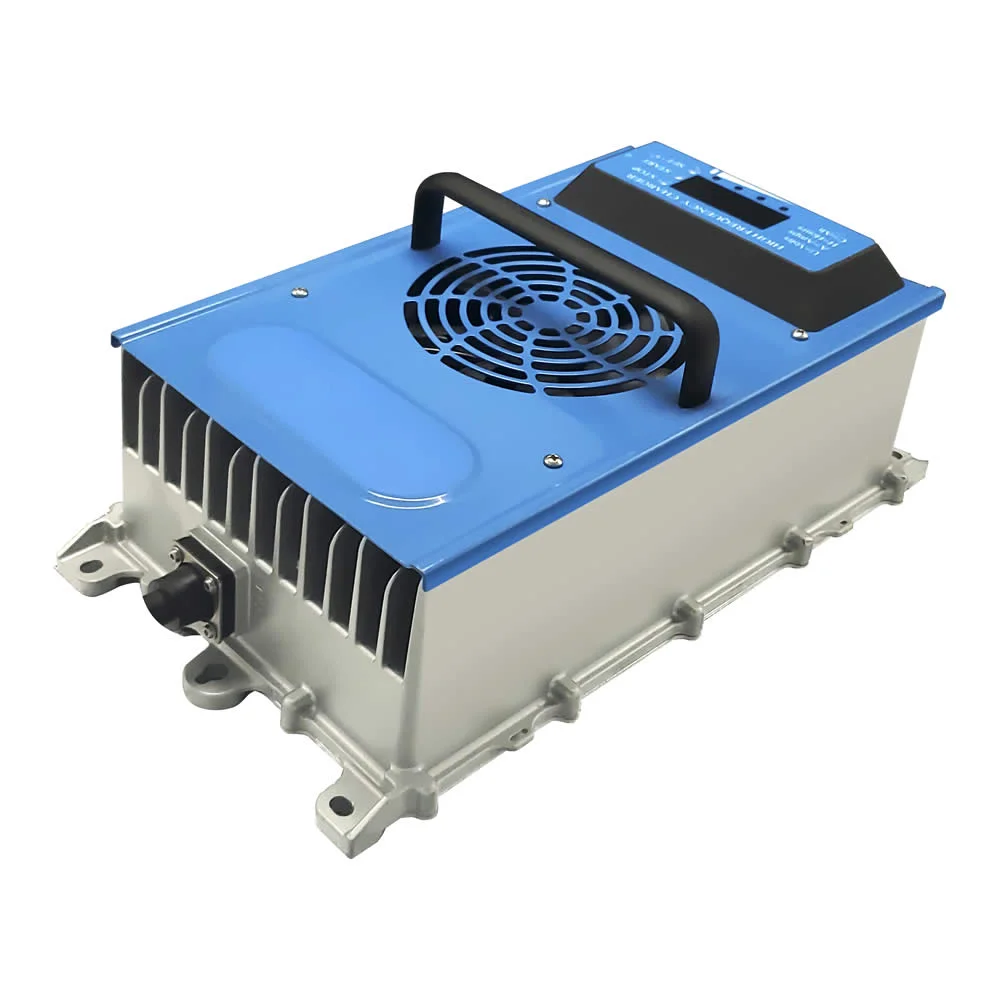
Exploring Wireless Charging Technology
Wireless charging, also known as inductive charging, uses electromagnetic fields to transfer energy from a charging station to an AGV without direct electrical connections.
How wireless charging works: An induction coil in the charging station creates an alternating electromagnetic field, which induces an electric current in a second coil in the AGV, charging its battery.
Key components: The primary components include the transmitter (charging station), receiver (AGV unit), and the management system that controls the charging process.
Types of Wireless Charging Systems
Wireless charging systems can vary based on their power output, efficiency, and the distance over which they can effectively transfer energy.
Description of each system with pros and cons: High-power systems can charge AGVs faster but may require more sophisticated cooling solutions. Low-power systems are more cost-effective but charge more slowly.
Advantages of Wireless Charging
- Allows for “opportunity charging” where AGVs can be charged during short downtime periods
- Eliminates wear and tear on physical connectors
- Enhances flexibility and efficiency in AGV deployment
Limitations of Wireless Charging
- Generally higher initial costs due to advanced technology
- Slightly lower energy transfer efficiency compared to wired charging
- May require more complex infrastructure integration
Comparing Wired and Wireless Charging for AGVs
The choice between wired and wireless charging for AGVs hinges on a variety of factors, including efficiency, cost, and operational requirements. This section compares these two charging methods across several critical dimensions.
Efficiency and Power Transfer
Wired charging typically offers higher energy transfer efficiency, whereas wireless systems have made significant advancements in closing the efficiency gap.
Installation and Maintenance Costs
Wired systems generally have lower upfront costs but may incur higher maintenance expenses over time. Wireless charging, while initially more expensive, offers potential savings in maintenance and operational flexibility.
Safety and Operational Reliability
Wireless charging reduces the risk of electrical faults and physical damage to connectors, enhancing safety and reliability.
Flexibility and Scalability
Wireless systems provide greater flexibility in AGV routing and scalability for expanding operations without extensive infrastructure changes.
Environmental Impact
Wireless charging can potentially reduce waste and environmental impact by eliminating the need for cable replacements and reducing the frequency of charging station maintenance.
Which Is Better: Wired or Wireless Charging?
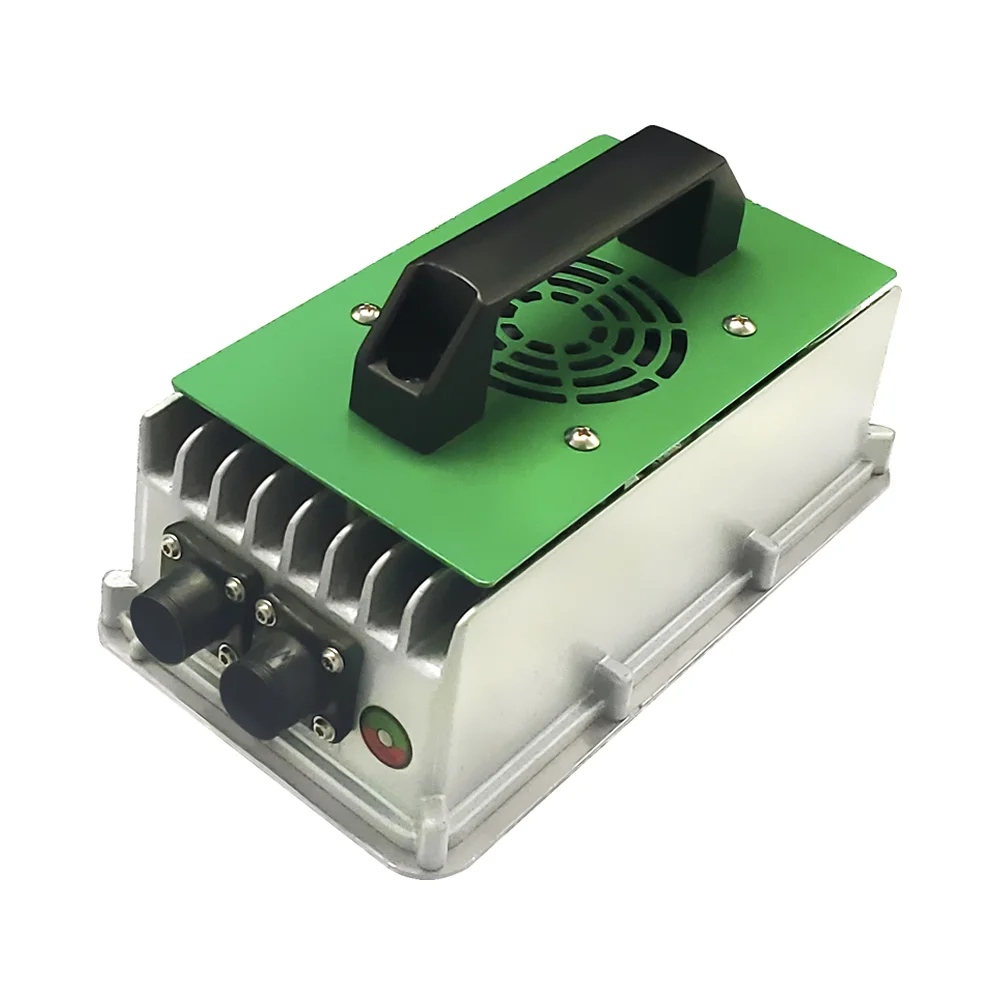
The decision between wired and wireless charging for AGVs is not one-size-fits-all. Factors such as operational environment, budget constraints, and future scalability play crucial roles in determining the optimal choice.
Factors to Consider When Choosing Between Wired and Wireless
Key decision factors include operational downtime tolerance, initial and ongoing cost considerations, and the desired level of flexibility and scalability in AGV deployment.
Use Case Scenarios for Wired vs. Wireless Charging
Wired charging may be more suitable for operations with scheduled downtime periods and limited routes. Wireless charging excels in dynamic environments where AGVs operate continuously across various paths.
Implementing AGV Battery Charging Systems
The successful implementation of an AGV battery charging system requires meticulous planning and consideration of operational needs.
Step-by-Step Guide to Implementing Wired Charging
Steps including planning, installation, and testing: Assessing power needs, selecting appropriate charging stations, integrating with existing infrastructure, and conducting thorough testing to ensure reliability and efficiency.
Step-by-Step Guide to Implementing Wireless Charging
Similar to wired charging, implementing wireless systems involves careful planning but also requires consideration of electromagnetic field interference and optimizing charging station placement for maximum efficiency.
Future Trends in AGV Battery Charging
Advancements in technology and increasing demand for efficient, sustainable operations are driving innovation in AGV battery charging methods.
Advancements in Battery Technology
Developments in battery materials and design are enhancing energy density, charging speed, and overall performance, further supporting the viability of both wired and wireless charging systems.
Innovations in Charging Methods
Research into higher-efficiency wireless charging and automated wired systems aim to reduce operational downtime and increase flexibility.
Integration with Renewable Energy Sources
The future of AGV battery charging is also intertwined with the broader adoption of renewable energy, offering opportunities to reduce the environmental impact of industrial operations.
Best Practices for AGV Battery Management and Charging
Effective battery management is crucial for maximizing the lifespan and performance of AGV batteries, regardless of the charging method.
Monitoring and Maintenance Tips
Regular monitoring of battery health and performance, adhering to recommended charging cycles, and conducting periodic maintenance can significantly extend battery life.
Safety Considerations
Ensuring proper handling and storage of batteries, following manufacturer guidelines, and implementing safety protocols for charging stations are essential for preventing accidents and ensuring operational safety.
Must Read: How to Finance a Car During a Recession
Conclusion
The quest for optimal AGV battery charging solutions reflects the broader challenges and opportunities in the realm of industrial automation. While both wired and wireless charging systems offer unique advantages and limitations, the decision ultimately hinges on specific operational requirements, financial considerations, and strategic objectives.
As technology evolves, the future of AGV battery charging promises further innovations and efficiencies, paving the way for even more dynamic and sustainable industrial environments.
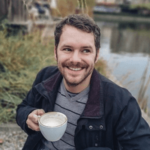
Harry O’Neill writes about all things tech, SaaS, and marketing at Solution Suggest. He’s known for turning complex ideas into clear, actionable insights. With experience working alongside top-tier companies worldwide, he helps brands connect with their audiences through content that drives real results.
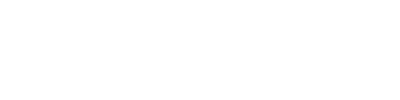