In a dangerous field like construction, safety management is a priority. Even with efficient construction scheduling software controlling the number of employees working, a serious or even fatal accident may occur at any given moment. Workers may fall off the scaffolding, and heavy materials can fall on them, or even be electrocuted by their machines. But with a competent safety manager and helpful project management tools, a lot of these accidents can be prevented and construction sites can be a little bit safer.
Even though an on-site safety manager is an additional cost, they can focus on keeping the site safe and the crew’s well-being protected, unlike project managers with a lot more to deal with. Paired with the best construction management software, safety managers can easily monitor the activities and see if they need any modifications.
Safety Leadership in Construction
Although construction safety managers are not safety leaders by definition, they certainly can be both– manage the crew while also leading them in safety. Essentially, managers use tools like subcontractor scheduling software to supervise the team, give orders, and occasionally make adjustments for better work performance. On the other hand, leaders influence the employees to willingly recognize and carry out the safety program to attain the team’s goal. With a proper builder schedule and good communication and interpersonal skills, instructions on safety can be disseminated thoroughly and effectively.
Duties of a Safety Manager
1. Looking for and addressing potential safety issues
Before construction on any structure may begin, safety managers look over the project and determine any safety hazards. Aside from surveying the area themselves, they also use technology, such as drones, to scout the place for issues that may need action. When they have assessed the project, they can start developing preventive solutions to answer the initial safety problems.
2. Evaluate active project sites
Once construction has begun, it’s the safety manager’s job to ensure that everyone stays on top of safety-related things. Specifically, they are tasked to:
- Make sure the crew and management are complying with the safety guidelines
- Note current safety issues
- Create and implement solutions to said problems with the help of management and field workers
- Organize and maintain paperwork on safety and training certifications
- Evaluate and modify safety policies and procedures
- Analyze and evaluate accident reports and case studies
3. Train and educate the management and crew
Construction safety managers are also responsible for educating the team on safety. As a preventive measure, safety managers and leaders conduct training sessions on safe work practices for the management and the crew. They also inform them of the safety policies and regulations to follow on-site. Included in this preventive practice is instilling the importance of wearing protective gear on-site and teaching the proper operation of tools and other heavy equipment.
It is also the construction safety manager’s job to sanction and discipline the people who fail or refuse to follow standard safety procedures.
Must Read: How to Be an Effective Construction Project Manager
9 Qualities and Skills of A Good Construction Safety Manager:
1. Goal-oriented
Even if they can think up several ways to prevent accidents, factors such as budgets and working conditions may hinder some of them from being implemented. That’s why construction safety managers should see the bigger picture and be realistic in creating plans and policies. More often than not, incident reductions come from simple but well-thought-out measures– focusing on the details will most likely lead to confusion and complications.
2. Sense of ethics
At some level, construction safety managers are responsible for the lives of the people on the project site. With that, they should be dedicated to keeping the workers safe and are committed to safety policy regulations. Above all, they must have a strong moral compass, always trusted to do the right thing, not the easy thing.
3. Knowledgeable in the trade and OSHA standards and regulations
There are days when the events are more fast-paced. During these times, they will not have time to leaf through their papers and books to tell them what they should or should not be done. So, aside from quick decision-making skills, they need to understand the field or trade they are working in and OSHA (Occupational Safety and Health Administration) guidelines. A good grasp of these is a must.
4. Excellent physical condition
Construction safety managers spend most of their time on their feet, walking around, and even climbing scaffolding and ladders to assess the area. So, they need the stamina to be able to go long periods and not easily get tired.
5. Detail-oriented
Construction is a large and complex industry to work in. With all the things going on- and off-site, safety managers must be careful and meticulous in doing their job. Overlooking even the smallest issues may lead to significant delays or accidents if not dealt with immediately.
6. Interpersonal and leadership skills
Construction safety managers should not be shy– dealing with people is a big part of their job. They must be dependable and responsible, as the workers’ lives are in their hands. Additionally, they should be able to productively work in teams, as a leader and a member.
However, getting along with the team is one thing, but it’s also vital for safety managers to be commanding and authoritative. If they are shy, quiet, or submissive, they will not take them seriously, leaving them as an ineffective leader.
7. Excellent communication skills
It’s right for any managerial position that communication is of utmost importance. Construction safety managers should be able to effectively convey the company’s safety policies, protocols, and procedures. This does not merely mean informing the team members, but the team should also understand and actively follow them.
On the same note, communication includes listening. Consequently, safety managers need to have top-notch listening skills to understand the sentiments of the crew.
8. Exceptional technical skills
While having knowledge of the field and regulatory concerns is good, it is not enough. Their understanding needs to be combined with hands-on experience to prevent future issues. Having done the documenting, reporting, and investigating past incidents can better equip them in dealing with current or future ones.
In addition to that, because they need to instruct the crew on properly operating the various machinery constructively, safety managers will need to understand how they work entirely. Their technical skills will help them know how the machine works, even if it’s new to them, they can teach how to operate it safely.
9. Sharp problem-solving skills
Construction workers will face many safety problems and it is the safety manager’s job to solve them. Listening, research, analytical, and decision-making skills will help them design safety policies and procedures that will be implemented to protect the employees from dangerous environments and situations.
Also Read: 10 Challenges in Construction Job Management and How to Solve Them
Tips for Becoming a Good Construction Safety Manager
Besides the qualities above, here are a few tips on becoming a good construction safety manager:
1. Lead by example
Management becomes more significant when leadership is involved. As mentioned beforehand, leaders influence their people’s behavior to achieve their goals. So by leading by example, the construction safety manager will show their subordinates how things should be. Also, employees learn more by observing rather than merely listening.
So, rather than just commanding or explaining, follow the rules you have set. You’ll have the others following in your footsteps in no time.
2. Praise safe employee behavior
Recognizing that a crew member has chosen the safe option and praising them encourages them to continue doing, then soon after, others will follow. Several studies have shown that positive reinforcement is more effective than the punishment of negative behaviors in disciplining employees.
3. Be open
Albeit in a managerial position, construction safety managers should be open to communicate with both the project management and the crew. Listen to their sentiments, ask them for suggestions, discuss their opinions, and observe their actions. Safety managers can learn so much just from the field workers because they know firsthand what’s going on. When they get enough information from them, they can continue doing their job by improving their safety quality. Plus, being open creates a better and more robust connection between them and the crew members.
4. Invest in the people
Professional duties aside, construction safety managers should care enough to go a bit farther than expected. The employees will appreciate even the littlest of things: lending them training materials like books or videos, bringing in special food for everyone, or just knowing their names. Simply showing kindness can build your reputation in the company, making you an even better safety manager than when you started.
You May Like: What Strategies Can Be Adopted to Make Online Classes Interesting?
Conclusion
Safety is an integral part of the construction industry. Without competent safety managers and concrete safety plans, the field will be more dangerous than it already is. To maximize effectuality, construction safety managers should possess several qualities that can make them better. It’s also essential for them to get to know the project’s ins and outs, including the design plan, the equipment, and the people.

Garrick Revels is the CEO of Pro Crew Software and a Certified Building Contractor at GCM Construction, a large concrete and foundation company in the Tampa Bay Area. With 18 years of experience in construction and a passion for technology was the catalyst for creating Pro Crew Schedule.
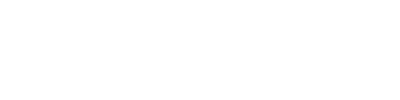