Metal fabrication is a complex and nuanced field requiring precise machinery and sophisticated techniques. Among the various tools employed, tandem press brakes stand out for their unique capabilities and advantages in handling large-scale components. This introduction delves into the essence of tandem press brakes, showcasing their fundamental purposes and basic functions within the industry.
What Are Tandem Press Brakes?
Tandem press brakes, unlike their single counterparts, consist of two synchronized press brakes that work in conjunction to handle longer or heavier pieces of metal. This arrangement not only increases the capacity of the machine but also enhances its flexibility and precision. Such a setup is pivotal for projects requiring extensive press work across large panels or sheets, making tandem press brakes a favored choice in heavy-duty metal fabrication.
How Do Tandem Press Brakes Work?
Before delving into the operational stages of tandem press brakes, it’s important to understand their design and functionality. These machines feature two independent, yet synchronized, brakes that allow operators to use them together for one long bend or separately for smaller jobs. This versatility is key to their functionality.
- Synchronization: Both brakes work in harmony, ensuring uniform pressure and bend accuracy.
- Control System: Advanced software controls ensure precise bending along the entire length of the material.
- Modular Use: Operators can engage one or both presses depending on the job requirements.
What Are the Main Benefits of Tandem Press Brakes?
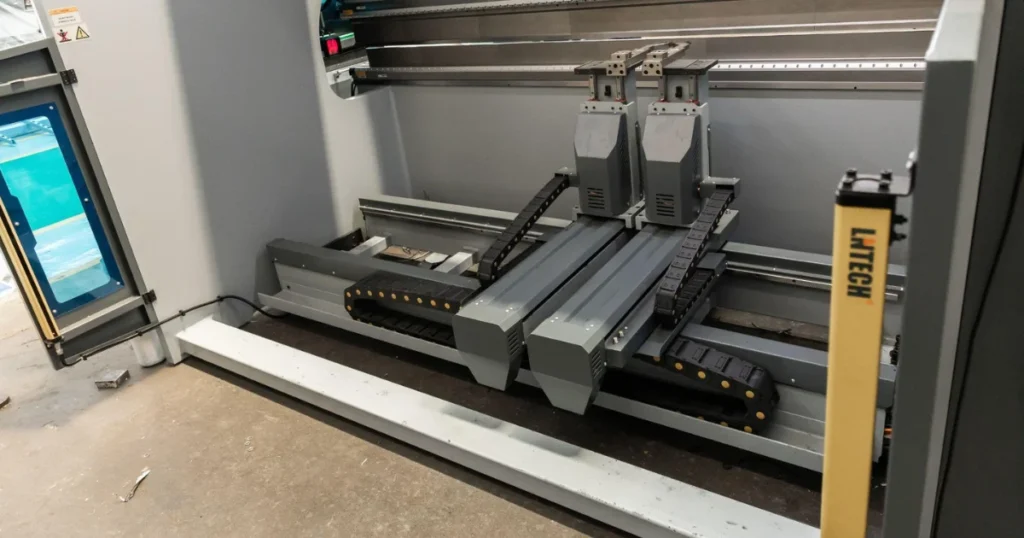
Utilizing tandem press brakes in metal fabrication brings several substantial benefits that enhance overall productivity and efficiency.
- Increased Productivity: The ability to bend long or thick materials quickly reduces project timelines.
- Flexibility in Handling Large Components: Adaptable setups mean that various job sizes can be accommodated easily.
- Higher Precision and Repeatability: Enhanced control systems ensure exact bends every time.
- Reduced Labor Costs: Automation and efficiency reduce the need for extensive manual input and oversight.
Must Read: How Remote Executive Assistants Transform Work Dynamics
Why Is Increased Productivity a Major Advantage?
In the realm of manufacturing, time is directly tied to cost. Tandem press brakes streamline processes and reduce the time taken for large-scale bending operations, thus significantly boosting production capacity without sacrificing quality.
How Does Flexibility Enhance Workflow?
The modular nature of tandem press brakes allows for adjustments based on specific project requirements. This flexibility is crucial for custom metal fabrication jobs that require varied bending lengths and thicknesses, ensuring that each piece is handled appropriately.
What Role Does Precision Play in Metal Fabrication?
Accuracy in metal fabrication is not merely a requirement but a necessity, especially in industries like aerospace and automotive where even a minor flaw can lead to catastrophic failures. Tandem press brakes provide the high level of precision needed for such critical applications.
What Types of Projects Benefit Most from Tandem Press Brakes?
Certain sectors particularly benefit from the specific capabilities of tandem press brakes:
- Aerospace Components: Where precision and size are both critical.
- Large-scale Construction Materials: Benefiting from the ability to handle big, bulky materials.
- Shipbuilding: Where large metal sheets are a common material.
Aerospace Components Manufacturing
In aerospace, the exactitude of every component is crucial. Tandem press brakes allow for the precise bending of large, complex pieces used in aircraft structures, ensuring they meet strict industry standards.
Construction Materials Fabrication
The construction industry benefits from tandem press brakes through the ability to quickly produce large-scale metal pieces that form the skeleton of buildings and infrastructures, ensuring speed and structural integrity.
Shipbuilding Industry
Shipbuilding requires the manipulation of extensive sheets of metal. Tandem press brakes excel in this area, providing the capability to bend large plates used in hull construction and other ship components.
Comparing Tandem Press Brakes to Traditional Press Brakes
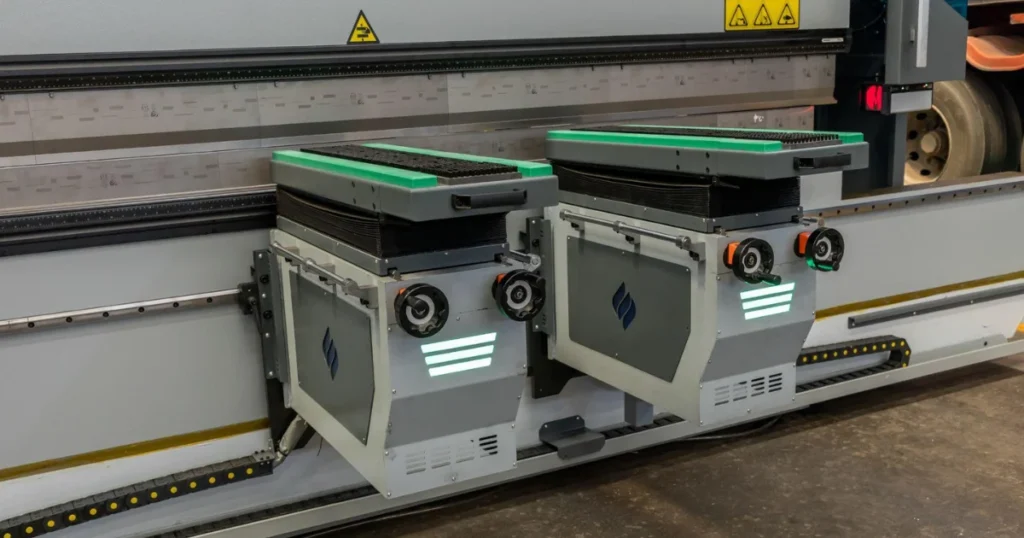
While traditional press brakes are effective for many projects, tandem press brakes offer distinct advantages:
- Capacity differences: Tandem models handle significantly larger and heavier materials.
- Efficiency levels: The dual setup reduces bending time and increases throughput.
- Application suitability: Tandem brakes are better suited for large-scale industrial applications.
When to Choose a Tandem Press Brake Over a Traditional One?
Choosing between a tandem and a traditional press brake often depends on project scale, material size, and precision requirements. For large, heavy, or complex bending needs, tandem is typically the preferred option.
What Are the Technical Specifications of Tandem Press Brakes?
Key specifications to consider when evaluating tandem press brakes include:
- Press Force: The maximum force that can be applied by the brakes, typically measured in tons.
- Working Length: The total length of the bending area, which dictates the size of the material that can be handled.
- Distance between Frames: Important for determining the flexibility and size of materials that can be accommodated.
How to Optimize the Use of Tandem Press Brakes?
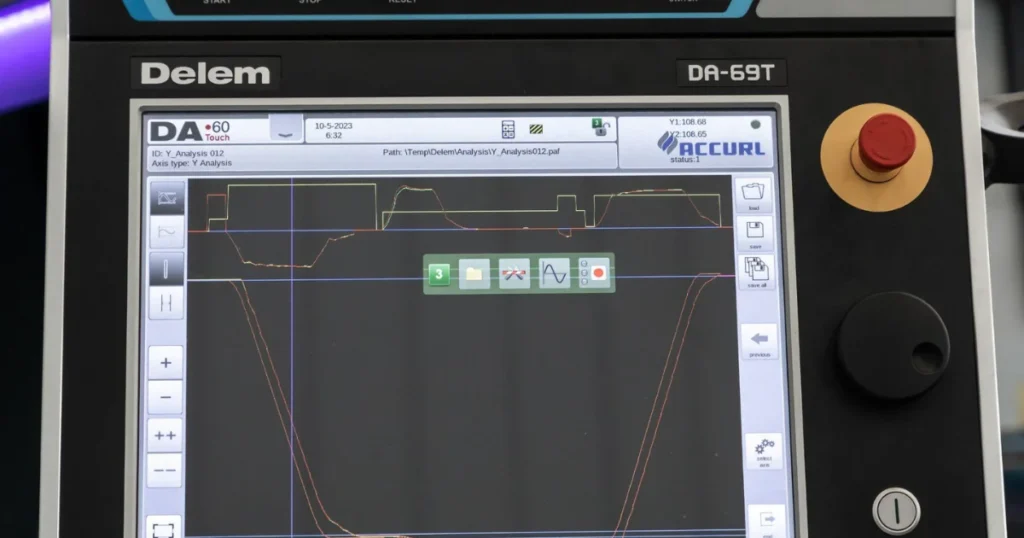
To maximize the effectiveness of tandem press brakes, follow these steps:
- Proper Setup: Ensure that both brakes are correctly calibrated and synchronized.
- Regular Maintenance: Keep the machines well-maintained to avoid downtime and ensure consistent performance.
- Skilled Operation: Train operators to utilize the full capabilities of the tandem setup.
Maintenance Tips for Tandem Press Brakes
Keeping tandem press brakes in top condition involves:
- Regular Lubrication: Essential for smooth operation and protection against wear.
- Routine Inspections: Catch issues before they lead to major failures.
- Component Replacements: Timely replacement of worn parts to maintain efficiency.
Safety Protocols for Operating Tandem Press Brakes
Ensuring operator safety is paramount:
- Comprehensive Training: Operators should be fully trained on the specific model of tandem press brake they will use.
- Protective Gear: Always use the necessary safety equipment, such as gloves and eye protection.
- Safety Features: Utilize the machine’s built-in safety measures, like light curtains and emergency stops.
What Are the Challenges Associated with Tandem Press Brakes?
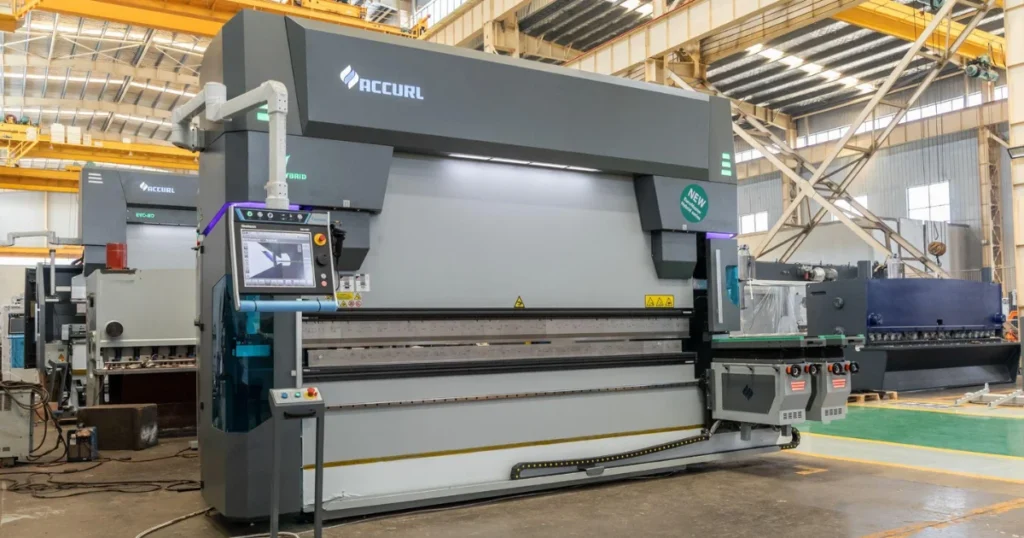
While tandem press brakes offer many advantages, there are also challenges to consider:
- Complex Setup and Calibration: Requires precise adjustment and understanding.
- Higher Initial Cost: More expensive than single press brakes due to their larger size and advanced features.
- Space Requirements: Need more floor space, which can be a limitation for smaller shops.
Case Studies: Success Stories Using Tandem Press Brakes
Several manufacturers have leveraged the power of tandem press brakes to achieve remarkable results. These case studies illustrate the practical benefits and transformative impact of this technology in real-world settings.
Future Trends in Tandem Press Brakes Technology
As technology evolves, so do the capabilities of tandem press brakes. Future developments are expected to include more automated features, increased precision, and enhanced safety measures, further pushing the boundaries of what can be achieved in metal fabrication.
See Also: Different Phases of Construction Project Management
Conclusion
Tandem press brakes represent a significant advancement in metal fabrication technology, offering enhanced efficiency, precision, and flexibility. Their impact on industries requiring large-scale metal bending is undeniable, and as technology continues to evolve, their role is set to become even more vital. This exploration not only underscores their current benefits but also anticipates future innovations that will continue to transform the field.
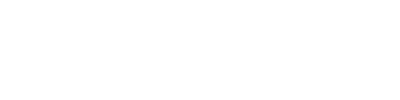